The "Lost Wax Method" is the only technique used by the artisans of Lotus Sculpture to create our Bronze statues. All of the artwork is one of a kind and is never reproduced on a large scale. Bronze casting in south India and Bangladesh is a skill passed on from generation to generation. Lotus Sculpture's artisans are the descendants of the famous
Chola and Pala schools of bronze casting of 8th to 13th centuries. Lotus Sculpture assures you that our sculptures are the best quality coming out India and Bangladesh today.
To give you an idea of the amount of time and delicate work that goes into the production of each piece we would like to outline the creation process for you. The lost wax method technique is divided into four distinct stages, namely 1) creation of the wax model 2) forming the mold around the wax model 3) casting of the mold and 4) finishing of the piece.
Although both Bengali and south Indian bronzes are cast using the lost wax method there are many differences in the two countries casting techniques which we will show here.
1) Creation of the Wax Model
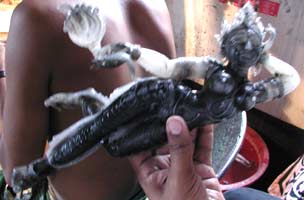
|
The first step in the process is to create a wax model. The wax model is an exact replica of what the finished bronze piece will look like. |
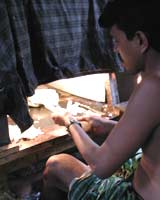
Here one artisan is shaping a leg with his fingers. One major difference between South Indian and Bengali artisans is that Bengalis use their hands more while South Indian sculptors use tools. |
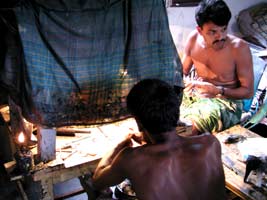
Two artisans usually work at a table together. The large sheet is used to trap the heat from the lamp, thus keeping the wax warm and malleable. |
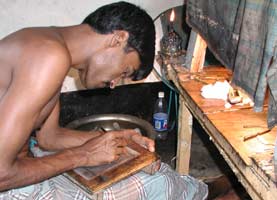
Bengali Artisan working on the base of a statue.
|
The Wax
In
Bangladesh a combination of 60% paraffin and 40% bee's wax is used to create the wax models. The wax is kept under a large light bulb, the heat keeping the wax malleable. Small quantities are taken to fashion the rough shape of the desired deity. |
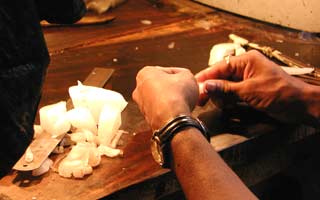
|
 |
Since it is more difficult to maintain the integrity of larger pieces, often the head, torso, arms, legs and bases are made separately. This allows for the fine details to be created without worrying about the model being maimed or destroyed. |
In
South India the percentage of bee's wax is greater giving the wax more of a golden coloration. Most or all of the work in the creation of the wax mold is done outdoors especially on larger pieces. This makes the artists very dependent on the weather. |
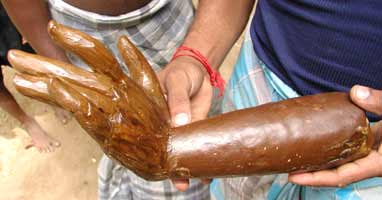
|
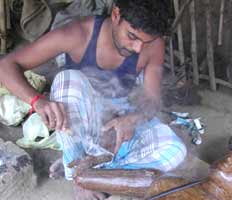
Smoke is created when the hot file touches the wax as the artist smoothes the file over the surface shaping the hand of Parvati. |
First the general shape of the model is produced in wax. Then a fire is used to heat a smooth, metal file. The heated file is then moved up and down the wax piece to shaped the details of the model. In larger pieces the details of the piece are done separately to maintain the integrity of the piece in the heat of India. |
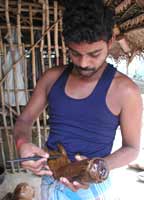
Dry filing is occasionally done to achieve the required appearance. |
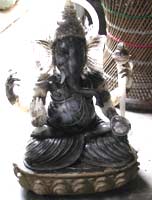
The wax mold of Ganesha. |
Once the various pieces are completed they are carefully assembled to form the final wax model. Using the flame of a lamp the connecting points are heated so that they can be melded together. With the artist's finger, the arm joints are smoothed to fit with the torso, and the torso smoothed to fit with the base. Once completed, the wax models are placed into water to ensure that they do not loose shape in the Asian sun. |
2) Forming the Mold
There are
three steps required to make the actual mold that covers the wax figure for casting of the bronze statues. The term "mold" refers to the hollow clay form that will be filled with molten bronze to form the figure. In the
first step, white clay known as "China Clay" is mixed with water to make a thin solution. This solution has a fine consistency which allows it to pick up the finer features of the wax model. This solution is then painted onto each wax model using a paintbrush and then allowed to dry for two days. This process is repeated twice. |
The first layer of china clay has been added to the wax mold of Shiva and Parvati. The first layer must be completely dry before the next layer is added. |
For the
second step, a one to two centimeter pasty mixture is applied to the outside of the model by hand. Once the paste is dried, holes are made at the bottom of the mold, which allow thin rods of wax, or nalis, to be attached to the wax base of the statue. Nalis serve as a passageway; they allow for the molten bronze to be poured into the mold and as an avenue for displaced air to escape out of the mold.
The wax model of Parvati has a Nali attached to its hand and leg which will help the flow of molten bronze during the casting process. |
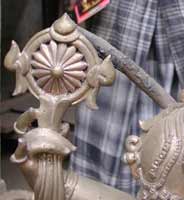
Above the Nalis are filled with bronze after the casting of the piece. The nali is later removed from the piece and then filed down. |
For the
third step, a third and final coating of rice husk, sand and clay is used to cover the entire surface of the piece. This is the final coating of the mold, applied to increase the thickness of the mold and to cover the nalis, which were inserted in the previous step. Small, cup like reservoirs are formed above each nali to allow for the metal to be poured into the mold without spilling it.
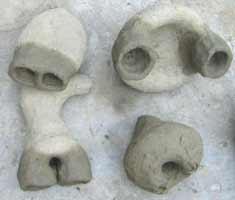
Bengali molds that are still drying.
Cup reservoirs are much larger for the Bengali molds. |
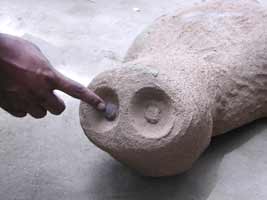
The south Indian artisan points to the wax nali that will be replaced by bronze during the casting process. |
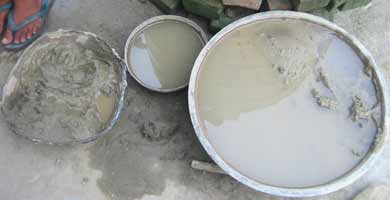
Above are the three different types of clay used to create the firing mold. The small middle bowl is used to hold the first layer. The large bowl on the right is used to hold the second layer, this is the largest layer comprising 60% of the layers on the entire piece. The last bowl on the left is used for the final layer and has the thickest consistency.
The Weather
The weather plays a very important part in the casting of pieces in both Bangladesh and in south India. It affects the whole process in two ways. The heat in both Bangladesh and south India is extreme. This often makes it very difficult to maintain the proper temperature for working with wax. During the hot season the wax is often too pliable to even hold a shape, making it impossible to sculpt the wax.
The monsoon season greatly affects the speed in which the molds dry. It is very difficult to dry large pieces because of the abundance of moisture in the air.
The artists of south India and Bangladesh have been casting bronze in these conditions for centuries and have found a way to work with the elements. During the rainy season the artists spend most of their time creating the wax models with limited time covering the molds and drying the molds. During the hot season they spend most of their time drying the various layers of molds and firing the ovens creating finished pieces. They are careful not to dry the molds in direct sunlight. The heat would damage the wax model inside the mold.
3) Casting the Mold
In reality, kings, the wealthy, and temples were the only people and institutions with enough money to create true, five metal (panchaloha), bronze deities. The five metals were gold, silver, copper, brass and lead. For contemporary bronzes; copper, brass and lead are the three main ingredients. Copper contains small amounts of gold and silver so technically today's bronzes are four metal bronzes. Copper is a necessary element in bronze because copper offers more malleability than other metals. This gives the sculptor a metal he can work with after the casting process to make the subtle alterations needed for a beautiful, finished piece.
As a general rule, approximately 220-260 pounds of bronze are cast at one time. The raw, unheated bronze is placed into egg shaped containers called crucibles. Bengalis use approximately 6-9 pounds of bronze in each crucible. South Indian artists use much larger crucibles. Once the molds and bronze containers are ready for firing, they are placed into the oven with the molds on the top and the containers on the bottom. The molds are positioned with the nalis facing downward allowing the wax to "burn out" after the oven is heated. Hence the name "lost wax method".
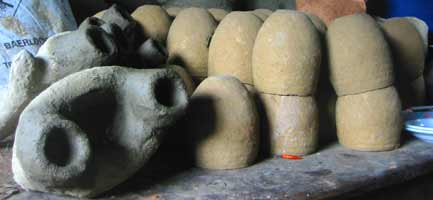
Bengali crucibles are noticeably smaller than south Indian crucibles. |
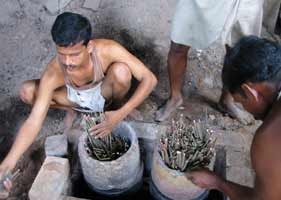
South Indian crucibles are much larger. Here artisans are shown filling the crucibles with various metals. |
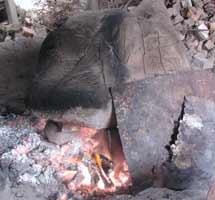
A 4 foot, 300 lbs bronze Ganesha is being fired in the picture above. Because of the size of the piece it cannot fit in a oven. It will have to sit on the fire for four hours so that all of the wax will melt out of the mold. |
To melt the bronze a temperature of at least 1800 degrees Fahrenheit is needed for approximately two to three hours. Once the firing is completed the molds are removed with the nalis facing upwards. Forceps are used to pick up the containers with the melted bronze so that the bronze can be poured into the molds through one of the nalis.
|
4) Finishing the Piece
After allowing the molds to cool for at least two hours, the bronze can be uncovered by chipping the layers of coating away. The entire statue is filed. There is almost always some small defect associated with the entire casting process. Air can be trapped in the mold creating a gap in the bronze or a piece can break off when the bronze is freed from the mold. Delicate reconstructive surgery takes place by heating up strips of metal to fill in the holes. This process is difficult and does not always succeed in solving the problem. For this reason a perfectly cast sculpture with no defects and perfect proportion is a prized piece since only masters of the art of bronze casting can achieve perfection in the entire process.
After being repaired and further filed down, the statue is sanded and buffed to remove any scratches and give the finished piece a shine. Care, precision, time and above all artistic ability are vital ingredients to practising the lost wax method of bronze casting.
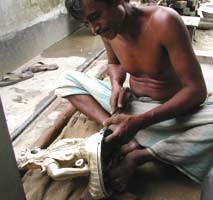
Post production filing. |
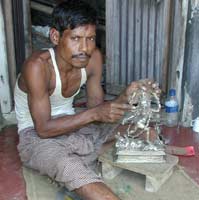
Post production filing on Kali. |
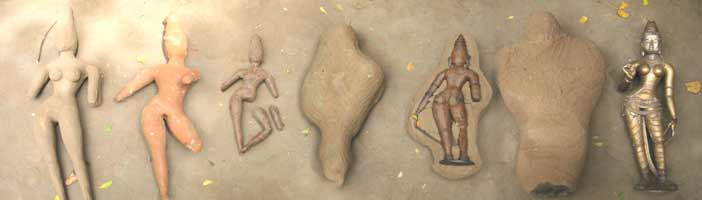
All of the stages of production for a larger south Indian lost wax piece (shown above).
It takes approximately 6 weeks to complete a 24 inch piece.
South Indian Bronze Artisans

|
Artisans of south India usually work in small groups called collectives, each collective is usually comprised of 3-8 artists. Each artist within the group has specific areas that they are proficient in. One person may be in charge of fashioning all the details of the piece, while another is in charge of shaping the general outline of the piece. All of the jobs are based on the skill of the artisan. |
To the right is a small collective of three artisans who I was able to spend time with on my last trip to Tamil Nadu. Arun on the left is the most gifted artist. He is responsible for the detail of all the wax models. Once the rough shape is made in wax, the piece is then given to Arun, he then works on finer details such as the shape of the face, the ornaments and the hands and feet. Raja in the middle is responsible for forming the rough mold for the piece. He does not have the artistic ability of Arun. Raja is the head of the collective and the sales person of the group, he is in charge of everything from acquiring raw materials to the sale of each individual piece to potential buyers like Lotus Sculpture. The young man, Kumar, on the right is an apprentice and helps with most of the labor involved with the piece. This mostly includes applying the various layers of molds to the outside of the wax model. He also helps with the basic shape of the piece. His skills are not yet developed enough for him to undertake the details of a piece. |
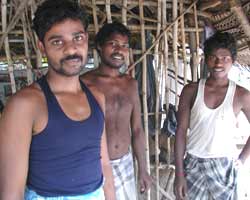
Arun, Raja and Kumar |
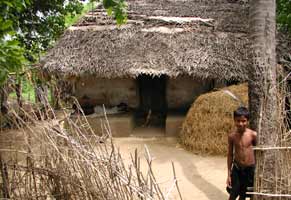
|
Because they are such a small collective they do not have an oven to fire their own pieces. Instead they plan the firing of all of their clay molds so that it coincides with the firing of a neighboring collective that owns a firing oven. Fire wood for a four hour fire is expensive and this helps both parties keep costs down by splitting the cost of the firing between two collectives. |
Above is their home which also doubles as their bronze studio. The boy is Raja's son who also helps with the work. He is destined to become a bronze artist like all of his ancestors before him. The caste system prohibits him from being anything other than a worker. Because of where he lives in Tamil Nadu his only real option is to become a bronze artisan like his father, which he looks forward to becoming.
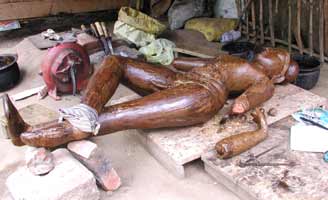
The collective was working on a large standing Shiva piece. They will be working on this piece for the next 6 months. They also work on smaller pieces so that they have some income to live on while they are completing this larger piece.
Written by Kyle Tortora founder of Lotus Sculpture with the help of Matthew Friedman and his book "Bangladesh Metal Casting" and the artisans pictured above. |
|